Maintenance
·
21 min read
What Is 5S in Maintenance?
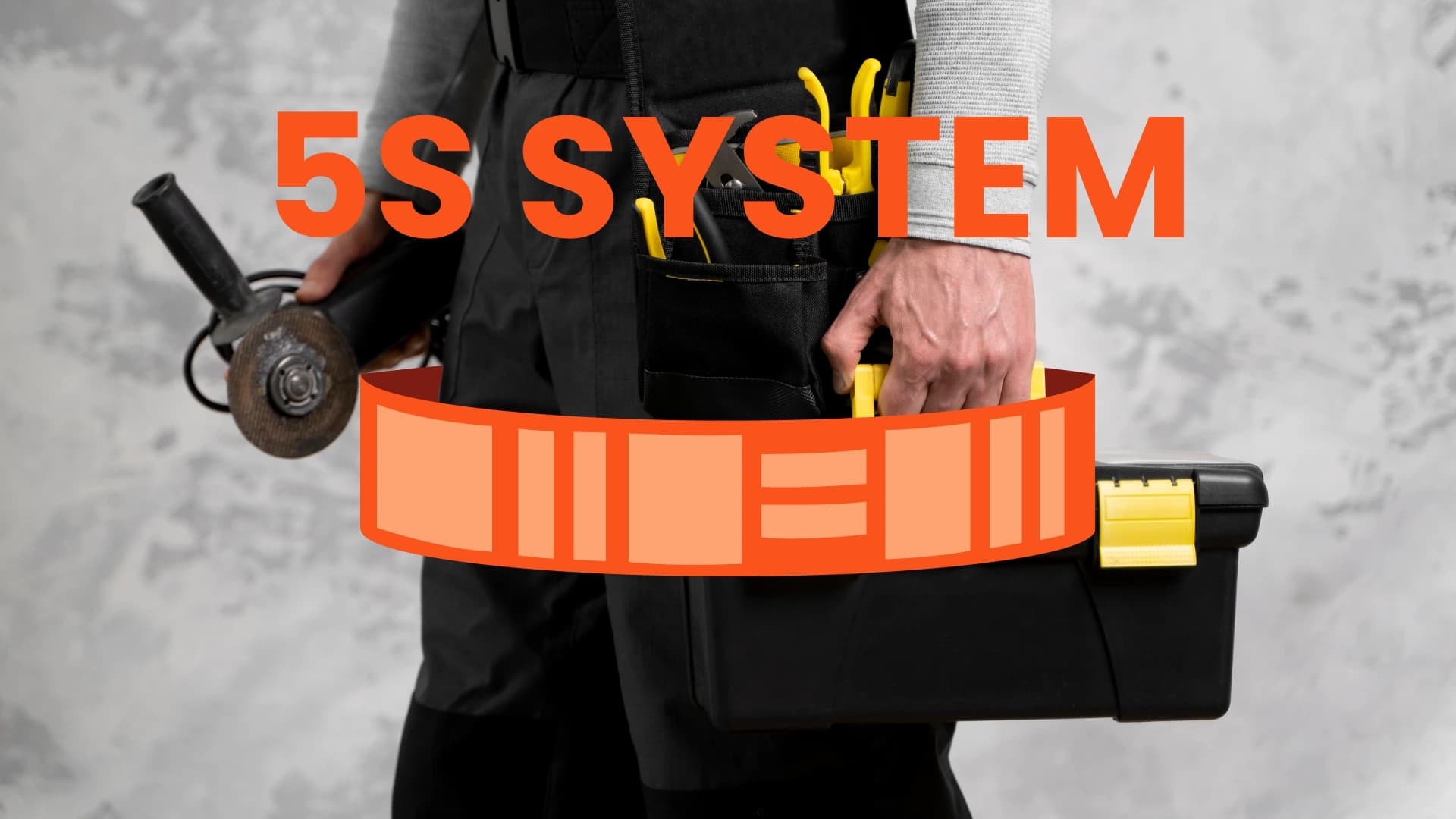
5S is a simple but powerful system which was originally developed in Japan as part of lean manufacturing. It helps teams to stay organized, work more efficiently, and prevent problems before they happen. Instead of adding more work to the team, it actually removes obstacles in your everyday activities.
If you’ve ever wasted time searching for a missing tool, stepped over stuff in the workshop or had an issue that could’ve been avoided, well truth is, you’re not alone. Maintenance teams are often under pressure and when things get busy, staying organized is usually the first thing to slip.
An example from one of our customers:
“We had three technicians searching for a torque wrench for 45 minutes… turns out it was under a pile of manuals, in the back of a drawer, labeled for HVAC.”
That’s nearly two hours of skilled time, just to find one tool.
If they only knew about the 5S method… But no worries. In this blog, we’ll break down each of the five S’s, show you how they apply to real maintenance work, and give you practical tips to make 5S part of your team’s routine.
And the best part? It’s easy to start, especially if you’re using a tool like Serwizz CMMS to support the process.
Where Did 5S Come From?
The 5S method started in Japan, mostly in factories like Toyota’s back in the 1950s. It was part of a bigger idea called “Lean Manufacturing” , which was all about cutting waste and working smarter, not harder. The five S’s are Japanese words that help teams keep their workspaces tidy and efficient.
Even today, 5S is used all over the world, not just in factories but also in maintenance teams, offices and anywhere people want to get organized.
Breaking Down the 5S Method: The Five Simple Steps
5S is about keeping your workspace clean, clear and easy to work in.
The 5S method consists of five steps and each step starts with the letter S. Basically, 5S is a simple way to minimize the chaos and make everyday maintenance easier.
Here is quick look of each step:
- Sort (Seiri): Get rid of what you don’t need
- Set in Order (Seiton): Give everything a proper place
- Shine (Seiso): Clean your space and your equipment
- Standardize (Seiketsu): Make the new way your normal
- Sustain (Shitsuke): Keep the habits going long term
Each one builds on the last. And when you put them all together, you don’t just get a cleaner shop: you get fewer breakdowns, less wasted time and most important: a team that works better together.
Next, let’s break down each “S” and show how it actually plays out in real maintenance work.
Step 1 – Sort (Seiri)
The first step in 5S is all about clearing out clutter. It means going through your tools, parts and equipment and deciding what’s really needed and what’s actually not needed at all.
In maintenance, well, just like in everyday life, it’s easy to hang on to “just-in-case” tools or old parts that rarely get used. But holding on to too much stuff can slow you down. You waste time searching and your workspace gets crowded and messy.
Sorting helps you:
- Find and keep only the tools and parts you actually use
- Toss or store away what’s broken, outdated, or unnecessary
- Free up space to work more comfortably and safely
A good tip is to involve the whole team. When everyone helps decide what stays and what not, it’s easier to keep the area tidy later on.
Using a tool like Serwizz makes sorting easier too: by tracking what you have, what you use most and when parts need replacing, you avoid buying duplicates or storing useless items.
Step 2 – Set in Order (Seiton)
Once unnecessary items have been removed through sorting (Seiri), the goal of setting in order is to establish a logical and structured layout that promotes ease of access, minimizes search time and enhances overall workflow efficiency.
“Set in order” means organizing your workspace so that tools, parts and equipment are easy to find, but also to put back. The goal? Less time spent searching, less walking back and forth and fewer interruptions during the job.
Here’s how this can work in a maintenance setting:
- Tool Shadowing: Give each tool a fixed spot: shadow boards or foam cutouts are great for this. If something’s missing, it’s instantly obvious.
- Workflow Zones: Break up your space into zones based on the kind of work being done. That way, tools and parts stay close to where they’re actually used.
- Visual Labels & Signage: Use clear labels, signs and color coding. If someone has to guess where something goes, the system’s not working.
- Ergonomic Layouts: Put frequently used tools within easy reach to cut down on movement and reduce fatigue, especially during longer jobs.
This step isn’t about being perfectly neat, it’s rather about making work smoother and faster.
Bonus tip: If a new team member couldn’t figure out where things belong within five minutes, it’s a sign your system needs tweaking.
Serwizz can help here too. You can tag equipment, track inventory, and even upload photos so your whole team knows what goes where and nothing goes missing.
Step 3 – Shine (Seiso): Don’t Let the Mess Build Up
This one’s simple: if your space is dirty, your equipment is going to suffer.
We’re not talking about deep cleaning or making the shop look pretty for a visitor. Shine means keeping things clean enough that you can spot leaks, wear, damage and deal with it before it becomes a real problem.
Grime hides issues. Dust clogs things up. Spills become slip hazards. Over time, mess turns into breakdowns.
What Shine Looks Like on the Floor
- Wipe down machines after use.
- Clean up oil, coolant, or debris right away, not “later.”
- Keep tools clean and check them as you go.
- Don’t let junk pile up on benches or carts.
- Take 30 seconds to look for damage or leaks while you’re cleaning.
It’s not about scrubbing everything spotless. It’s about keeping your gear in good working shape.
The biggest mistake? Leaving cleaning as “someone else’s job.” That’s when it falls apart.
Here’s what actually works:
- Add simple cleaning tasks to daily routines: before or after jobs, or during shift handoffs.
- Use checklists to keep it consistent. Doesn't have to be fancy, just clear.
- Assign areas or machines to specific people so everyone knows what they’re responsible for.
- Do a quick weekly check to see how things are holding up.
One of our users told us they started doing a 3-minute clean-up before lunch and before clocking out. Just a habit, nothing formal. A few weeks in, they had fewer safety issues, fewer tool replacements, and faster response time during breakdowns.
Why? Because the mess wasn’t getting in the way anymore.
With Serwizz, you can add those cleaning tasks right into work orders, link checklists to assets and keep track of who did what. It helps make Shine a habit, not a once-a-month panic clean.
Step 4 – Standardize (Seiketsu)
Getting organized is one thing. Staying that way? That’s where the real work starts.
Standardizing means taking what’s working: the sorting, the clean workspace, the routines and turning it into a system the whole team can follow. No guesswork, no “I thought you were doing that” moments. Just clear steps, done the same way every time.
Start by writing out how the job should be done. Think of it as a recipe:
- What tools do you need?
- What’s the safest way to do it?
- Any checks to make before or after?
- Is there anything the OEM says you have to do?
Make it simple and to the point. Add photos if you can. Nobody wants to read a bunch of text when they’re standing in front of a machine.
Once you’ve got the steps written down, turn them into checklists. Checklists help make sure nothing gets missed.
Can’t remember what to check on that old pump? It’s on the list.
Need to double-check a few safety steps before starting a job? List’s got you covered.
You don’t have to rely on memory, and you don’t waste time guessing. Just follow the list and get on with the job.
With Serwizz, you can attach those checklists right to a task or asset, so techs have everything they need right in front of them: no second-guessing.
Step 5 – Sustain (Shitsuke)
The truth is: anyone can clean up a shop once. The hard part? Keeping it that way a month from now.
Sustain is about building habits that last. Not just rules on paper, but a real mindset shift where staying organized becomes part of how your team works, not a “one-time project” or something only done when the boss walks through.
You’ve already put the effort into sorting, setting up, cleaning and standardizing. Now the goal is to keep it going, day after day. Here’s what helps:
- Quick check-ins and audits: Doesn’t have to be formal. A simple walk-around to see if tools are back in place or if anything’s starting to slide.
- Team feedback: Let the crew speak up. If something’s not working, they’ll notice it first. Make it easy for them to suggest better ways of doing things.
- Set a few simple KPIs: Track things like time lost to searching for tools, time between failures or number of safety issues. Soon you will notice if 5S is making a difference.
To really stick, 5S needs to be more than a “maintenance thing.” It should be part of everyone's working culture, from new hires to your most experienced techs.
- Train the new employees early: Make 5S part of onboarding. How we do things around here.
- Keep it visible: Post simple reminders. Use labels. Show before-and-after photos. Make it clear what “good” looks like.
- Lead by example: If team leads and managers stick to the process, the rest will too.
- Celebrate wins: When a team keeps their area in shape, hits a KPI or improves a process: give them credit. Doesn’t have to be fancy, just a “good job” and a bit of recognition goes a long way.
Processes change. Equipment gets updated. People come and go. The point of Sustain isn’t to freeze things forever. It’s a continuous improvement thing, not just one hit wonder.
With Serwizz, it’s easier to track your 5S progress, assign recurring checklists, gather feedback and ensure the standards grow.
Benefits of 5S in Maintenance
Making time for 5S isn’t extra work, it pays off sooner or later. Here’s what teams see when they stick with it:
- FindTools and Parts Fast: No more digging through drawers or hunting down parts. Teams report significantly less time wasted searching. It’s a real boost when you're in the middle of a job
- Catch Problems Before They Break: When everything’s visible and you’re keeping things cleaned and sorted, small issues will eventually stand out. That means fewer surprise breakdowns .
- A Safer Work Zone: Clutter and mess lead to slips, trips or accidents. A clean, organized area makes it easier to move around and spot hazards before someone gets hurt .
- Better Work Quality: When routines are clear, tools are reliable, and the space is organized, jobs get done right the first time. Standardized processes mean fewer mistakes.
- Less Waste and Lower Costs: No overbuying spare parts or supplies. With a neat storeroom and parts you actually use, inventory stays in check and expenses go down .
- Equipment Lasts Longer: Machines that are regularly cleaned, inspected and used correctly tend to break down less. That means more uptime and less emergency repair work .
- Team Pride and Efficiency: A clean shop sends a clear message: you care. Teams feel more ownership and satisfaction when the workspace is organized and reflects their effort
A reliability manager shared how a simple 5S clean-up transformed a lathe area. The toolmaker took pride in the neatness, they built momentum and that little action sparked a shift across the whole shop.
Another team we worked with tracked fewer tool searches and faster fix times after adding a 2-minute clean rule. Uploading photos of their clean zone helped them see progress.
Common Roadblocks with 5S and How to Get Past Them
Let’s be real, keeping up with 5S can be hard, especially in maintenance where things move fast and surprises happen daily. It’s normal to hit a few bumps. What matters is how you respond.
Here are the most common roadblocks maintenance teams face and how to fix them.
1. “We Don’t Have Time for This”
When things get busy or you're short on people, staying organized can become a challenge.
Solution: Start small. Pick one cabinet or station and fix just that. You don’t need to shut down the shop to make progress.
2. “We Tried 5S Before… It Didn’t Stick”
Maybe you gave 5S a shot before. Things looked great for a few days, you’ve put labels, sorted the tools, but then everyone got busy and it slowly went back to how it was.
Solution: Use checklists, photos or quick reminders to keep everyone on track. Use a tool like Serwizz to create visual “before and after” boards, assign repeat tasks or log photos of completed checklists. These things help people stay accountable and proud of their work.
3. “People Don’t Follow the System”
You’ve labeled every drawer, but tools still disappear. The tape lines get ignored. It feels like no one’s sticking to the plan.
Solution: Make the system easy to follow. If the storage setup doesn’t make sense to the people using it, they won’t use it. Let them own their spaces. Listen to their suggestions. People support what they help create.
4. “Too Many Tools, Not Enough Space”
If your storage areas are overflowing or you’ve got five versions of the same spanner, it’s tough to get organized.
Solution: That’s where Sort (the first S) comes in. Get rid of what you don’t use, and store the rest based on frequency. Daily-use tools should be within arm’s reach. Rarely used gear can go higher up or in deeper storage.
5. “People Don’t See the Point”
If 5S feels like “extra work” with no clear benefit, it’s hard to get buy-in.
Solution: Show the wins. Did a technician find the right part faster? Did you avoid a repair because something was caught during cleaning? Share it. Small wins build motivation.
Tracking Progress: How to Know 5S Is Working
So, you’ve cleaned up the workspace, added some labels, and tools finally have a home. But how do you know if 5S is really making a difference?
It’s not always about charts or reports, sometimes the best signs are right in front of you. Here are some good examples:
- Fewer missing tools: If your team isn’t wasting time hunting for gear, that’s a win.
- Faster jobs: When everything’s where it should be, tasks get done quicker.
- Cleaner, safer spaces: Less clutter means fewer accidents and a smoother flow.
- Less grumbling: You’ll hear fewer complaints like “Where’s the wrench?” or “Who left this mess?”
Sometimes, no feedback is good feedback.
Few ideas how to track the progress:
- Before-and-After Photos
A picture really can say more than a spreadsheet. Snap a quick “before” photo of a tool area or storage cabinet. A few weeks later, take another. If things still look organized, 5S is working.
With Serwizz, you can upload and track those images right inside your checklists or maintenance logs. Simple, visual proof.
- Spot Checks or Mini-Audits
You don’t need a clipboard army. Just pick a few key spots (like the tool wall or parts shelves) and give them a quick look now and then. Are things where they should be? Still labeled? That’s a simple way to keep tabs without making it a big task. - Use Simple Metrics
- Time saved on common tasks
- Number of missing or misplaced tools
- Downtime due to disorganization
- How often checklists or cleaning tasks are skipped
Even just tracking one or two of these each month gives you a feel for how things are moving.
- Ask the Team
It’s easy to overlook this, but just asking, “Is this working for you?” goes a long way. Your team will usually tell you if something’s helping — or if it’s just becoming noise.
Tips to Make 5S Work in Your Maintenance Department (with Serwizz)
If you're just getting started with 5S, don’t worry, it could be overwhelming. But no worries, you can achieve good results by implementing small changes and continue from there. That’s where Serwizz can really help.
- Start with One Area
- Pick one spot: ie a tool cabinet. In Serwizz, you can create a checklist just for that area and assign it to your team. Easy to follow, easy to track.
- Build Simple Habits
- Use reminders and checklists to keep everyone on the same page without needing constant micromanagement. Serwizz lets you set repeating tasks. In that way things like “clean station” or “check tool storage” show up automatically.
- Use Photos to Track Progress
- Take a before-and-after photo when you organize an area. You can upload those photos straight into Serwizz, right inside your task records.
- Get the Team Involved
- Serwizz lets team members leave comments, attach notes or flag issues so improvements don’t get lost.
5S doesn’t have to be complicated. With a few simple steps, the right tools and a team that’s on board, you can avoid a stressful situation in your everyday maintenance.
Serwizz is here to support you every step of the way. Start small. Stay consistent. Keep improving.