Automotive Manufacturing Maintenance Software
Automotive Maintenance & Work Order Software
Simplify fleet and workshop management with a digital platform for automotive service providers. Track work orders, monitor vehicle maintenance, and improve efficiency in repairs, inspections, and routine servicing.

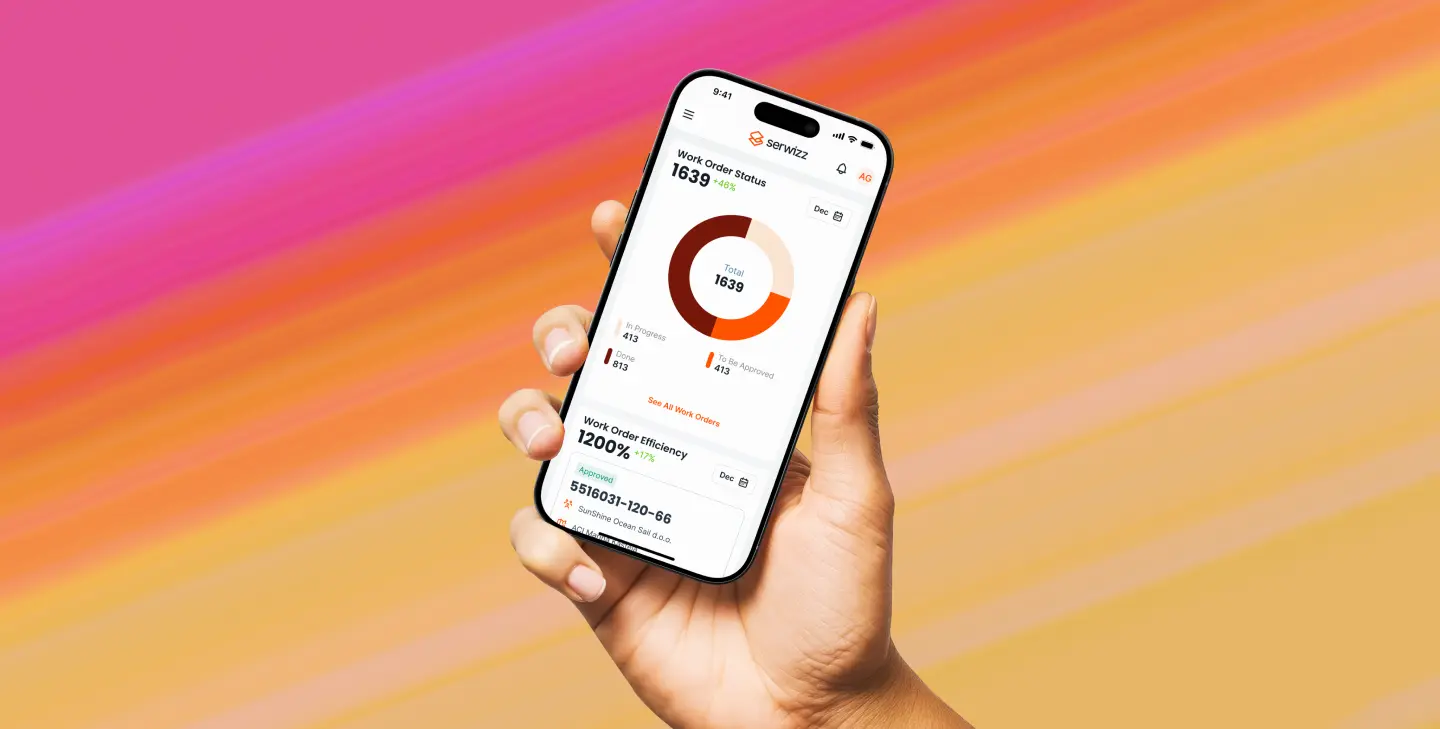
Work Order Tracking Software Features
Our mobile-first work order software helps maintenance teams stay productive in the field with real-time updates, digital approvals, and smart tracking features.
Work order approvals
Capture electronic signatures
Automate your digital work order
Real-time notifications
Include photos & documents
Analytics support
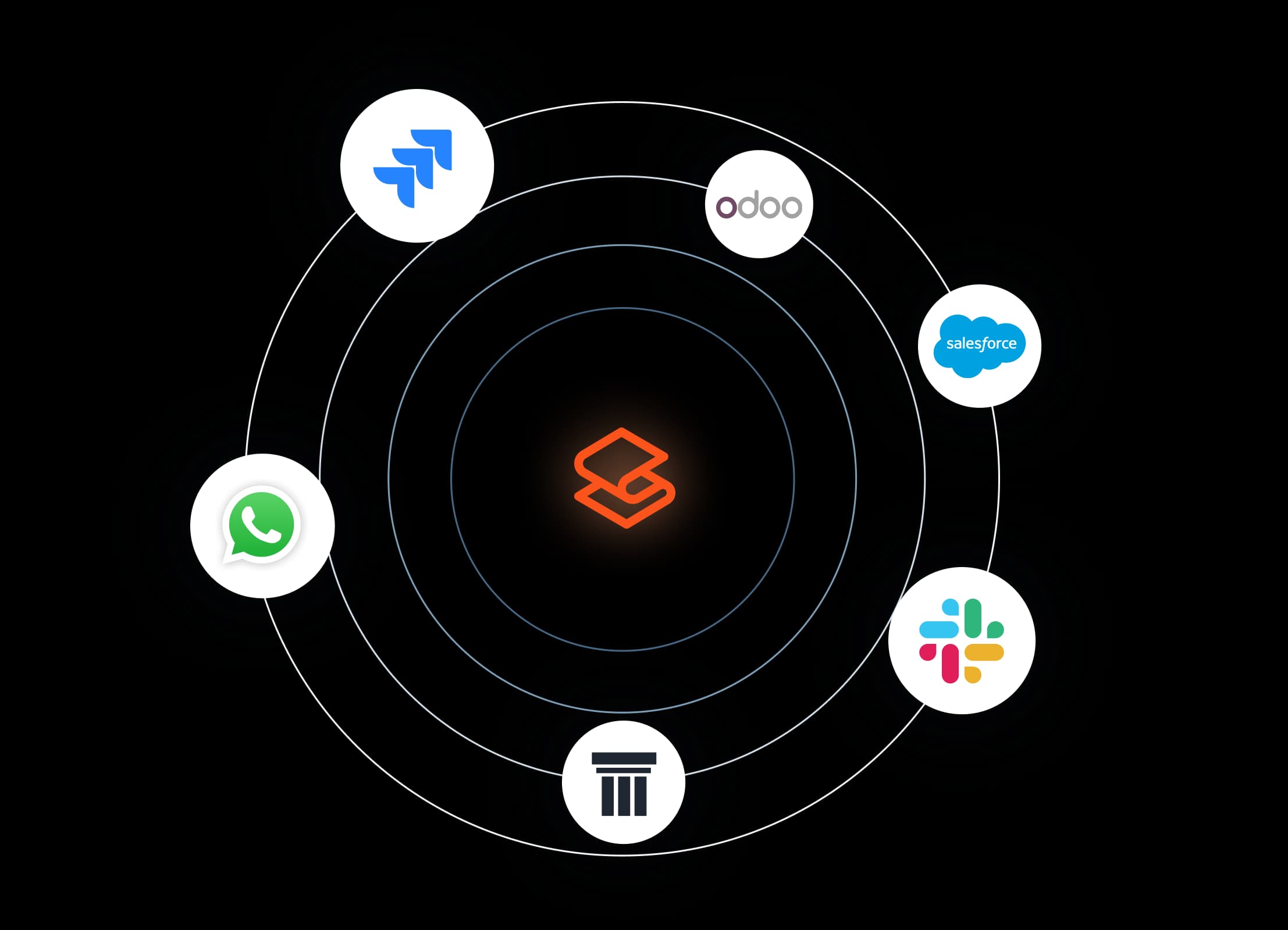
One 💰 price for all
Get all CMMS features with simple, transparent pricing. No hidden tiers - just one plan, monthly or discounted annually, for businesses of any size.
Top CMMS questions answered
Explore answers to common questions about maintenance software and digital workflows.
CMMS platforms are widely used across industries such as manufacturing, healthcare, facilities management, utilities, and logistics. Common users include maintenance managers, technicians, operations staff, and facility teams responsible for asset upkeep and compliance.
Key benefits of using a CMMS include minimised equipment downtime, improved asset performance, optimised maintenance scheduling, better spare parts management, and enhanced compliance. CMMS tools also support data-driven decisions with built-in reporting and analytics features.
By automating tasks like work order creation and maintenance scheduling, a CMMS simplifies daily processes. It provides real-time visibility, centralises critical information, and ensures maintenance activities are prioritised efficiently across teams.
Most CMMS platforms offer asset tracking, work order management, preventive maintenance scheduling, inventory control, mobile access, system integrations, and analytics dashboards to support maintenance planning and performance reviews.
Absolutely. Small businesses benefit from a CMMS by gaining control over maintenance workflows, reducing unplanned downtime, and scaling operations effectively—all without requiring large teams or resources.
A CMMS can automate inspection schedules, maintain digital audit trails, and standardise safety procedures. This supports regulatory compliance and ensures timely maintenance of safety-critical equipment.
Many modern CMMS solutions are cloud-hosted, offering advantages such as remote access, real-time updates, lower infrastructure costs, and easy scaling across multiple sites or teams.
While both systems manage assets, CMMS tools focus on day-to-day maintenance operations. EAM systems, or Enterprise Asset Management platforms, offer broader capabilities, including full lifecycle asset planning and strategic asset investment decisions.
When selecting a CMMS, consider factors like your team size, industry needs, system usability, reporting capabilities, integration support, vendor reputation, and available training and support services.
Implementation timelines vary based on the complexity of your operations and number of users. Generally, rollout can take anywhere from a few weeks to a few months, factoring in setup, data migration, training, and testing.
Training typically involves onboarding for administrators and maintenance users, followed by periodic updates for new features and workflows. Most providers offer hands-on sessions, documentation, and ongoing support.
Costs depend on your organisation's size, required features, and deployment model. Typical expenses include software licenses, setup and training, ongoing support, and optional hardware. Prices can range from a few thousand to several hundred thousand dollars annually.