MRO
·
15 min read
Maintenance, Repair, and Overhaul (MRO) Explained
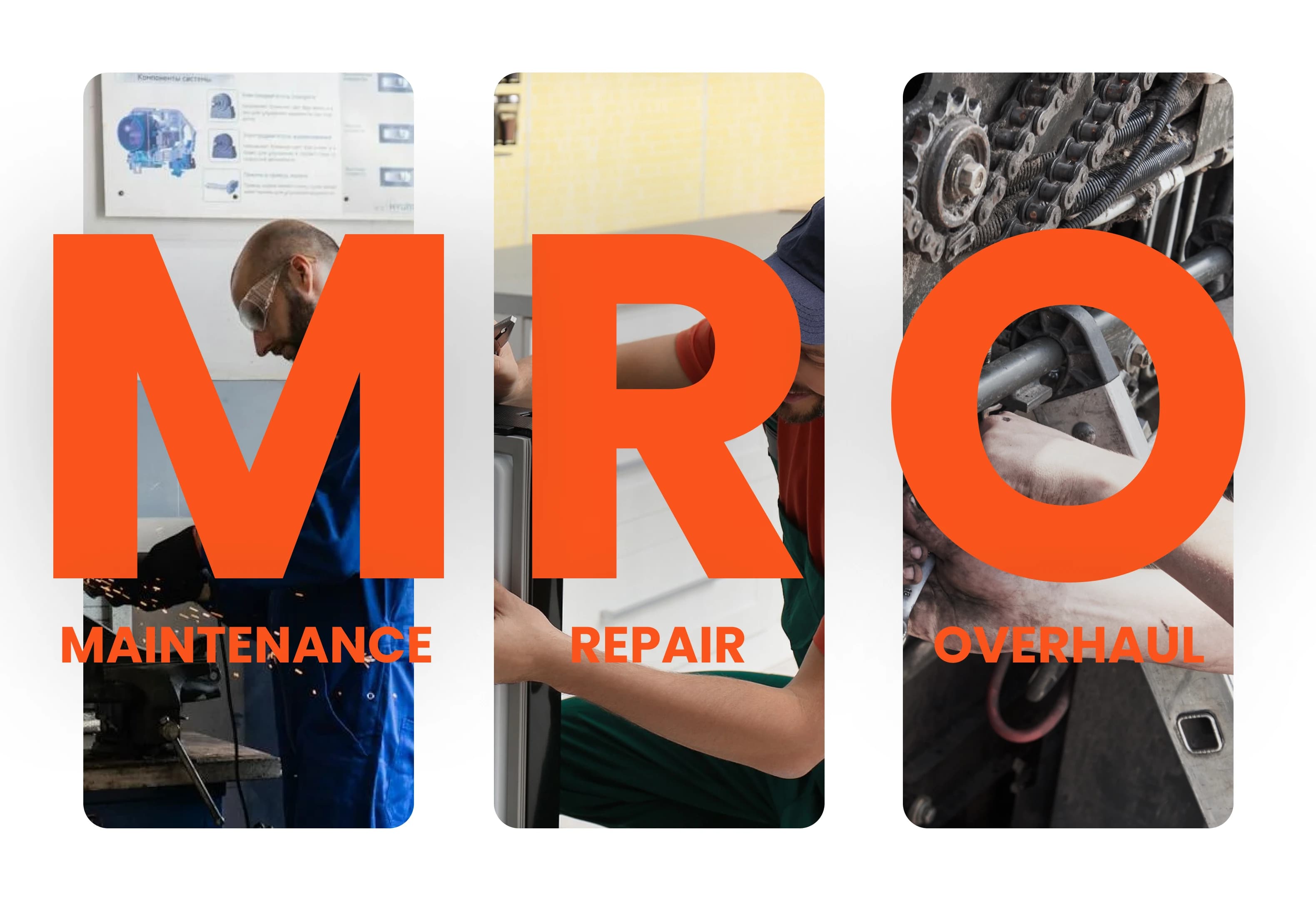
What is MRO?
MRO stands for Maintenance, Repair and Overhaul. It is the one of the most important parts of any asset operation.
Think of MRO as everything that keeps your machines, equipment and infrastructure running. It’s the spare parts you keep in the warehouse, the technician tightening bolts during a scheduled checkup or the emergency fix when something breaks down at 2 a.m. If maintenance is the “what,” MRO is the “how.”
MRO covers the following:
- Maintenance: Regular upkeep to prevent breakdowns.
- Repair: Fixing issues when something doesn't work.
- Overhaul: A more complete rebuild or deep service to extend the life of a machine.
MRO is all about extending the life and performance of what you already have. It’s not always glamorous work, but without it, operations grind to a halt.
You’ll find MRO in all kinds of industries: manufacturing, logistics, energy, healthcare and more. Anywhere there’s equipment that needs to run, MRO is involved.. And yet, it’s often in the background, underfunded, under-planned or treated like an afterthought.
That’s where things go wrong. Without a solid MRO strategy, organizations end up with costly downtime, reactive firefighting and overstocked or empty warehouses.
To sum up: MRO is not just about fixing what’s broken. It’s about making maintenance smarter, faster and for sure more cost-effective. MRO does all that while keeping business moving.
Where is MRO Used?
MRO shows up in every kind of maintenance work - no matter if it is planned weeks in advance or something that comes up unexpectedly. If a team is maintaining or fixing equipment, MRO is part of it.
We will show the usage of MRO within the three maintenance types.
Preventive Maintenance
Preventive maintenance (PM) is the routine maintenance of assets and equipment to reduce equipment failure, maximize uptime and optimize long-term asset management.
Since we are talking about the scheduled, planned work, MRO helps us prevent the problems before they even happen. If your team is aware of upcoming inspection, change of the filters or cleaning tasks, they would like to have supplies ready. If you don’t have the right supplies ready, your task might last much more than you would like to and cause unnecessary delay. That’s where MRO helps - it ensures you have the right supplies already in the stock.
Predictive Maintenance
By the definition, predictive maintenance uses time series historical and failure data to predict the future potential health of equipment and so anticipate problems in advance. In short, you will use the historical data to decide when to act. For example sensors might show that a motor is starting to overheat or vibrate more than normal. This is the signal for you to check or replace it.
How does the MRO fit here? Well, even with good data, you will be able to fix the issue, only if you have the right parts ready. MRO needs to keep up with what predictive tools are telling you.
Corrective Maintenance
Corrective maintenance is the category of maintenance tasks that are performed to repair faulty systems and equipment. In short, we need to fix something that is already broken. In most cases, these tasks are not just unplanned, but also urgent.
For corrective maintenance MRO is critical. The faster you can get the part and tools, the faster things go back online. If you have to wait for the delivery of broken parts, the downtime will be increased.
Managing MRO Inventory: A Balancing Act
MRO inventory isn’t just about filling shelves with spare parts. MRO should help you to have what you need, when you need. It should also help you reduce the downtime or spend too much time finding the right part.
You and your team might have to find the balance between too much or too little stock. If you have too much stock, you are using too much space, spend too much money and you have unused parts for years, which is for sure not good. In case you have too little stock, you could face the delays or too long downtime, which will lead to client dissatisfaction.
What Does MRO Inventory Include?
MRO inventory can include:
- Bearings, belts, gaskets, fasteners
- Tools, lubricants, cleaning supplies
- Safety gear
- Manuals or calibration kits
Basically, anything your team needs to maintain or fix equipment.
Where It Often Goes Wrong
- No clear system – Parts are stored in random places or tracked on paper (if at all).
- Duplicate items – Same part ordered multiple times because no one knew it was already in stock.
- Critical items missing – A single missing gasket can hold up an entire job.
- Poor communication – Maintenance, purchasing, and finance aren’t always on the same page.
How to Keep It Under Control
Managing MRO inventory well doesn’t have to be complicated, but it does take some consistency:
- Organize your storeroom – use labels and clean layout.
- Use a CMMS or tracking system – A simple digital tool such as Serwizz can help you avoid duplicate orders.
- Set min/max levels – Reorder when stock gets low, not when it runs out.
- Review regularly – Some items get used constantly, others almost never. Don’t just set it and forget it.
Challenges in MRO
MRO might sound simple on paper. It says just keep the right parts and tools available. But in practice, it’s a constant battle between time, budget, space and communication.
Here are some of the most common issues teams run into when dealing with MRO:
1. Inventory is a Mess
It’s one of the biggest and most common problems. Parts stored in random places. No labels. No system. Things go missing. You order what you already have or worse, you don’t have what you need during a breakdown.
2. Lack of Standardization
If you don’t track things, you could end up having the two identical machines, but each one uses different spare parts. Different teams or even team members order different brands for the same component. Over time, this turns into a storeroom full of duplicates and confusion.
3. Poor Communication Between Departments
Maintenance needs a part urgently but maybe the purchasing isn’t aware or finance won’t approve it in time. Different teams are working without collaboration, and that slows everything down.
4. Supplier Delays or Stockouts
Even if your internal system is solid, the issues might come from the external. Maybe the delivery is delayed or the price has gone up. If you rely too on just one supplier, you could be more affected.
5. Outdated or Manual Tracking
Spreadsheets or paper logs might work for a while, but they don’t scale. You end up guessing what’s in stock or walking to the warehouse to check. Manual or paper logs take tame and lead to mistakes.
6. Budget Constraints
MRO usually doesn’t get a big slice of the budget. It’s seen as a cost, not a priority. But once something breaks and everything stops, you realise how important MRO is. Keeping stock levels balanced while staying within budget is a constant challenge.
The Benefits of a Well-Run MRO Process
When MRO is managed properly, a lot of things get easier. Workflows are smoother, downtime is shorter and the whole maintenance operation feels more in control.
Let’s see some of the benefits of the MRO:
1. Less Downtime
With MRO in place, you can avoid the situations when you lose hours or days getting something that you don’t have in stock. When parts are easy to find and tools are ready, maintenance gets done faster, regardless if it's a routine job or an emergency fix.
2. Fewer Last-Minute Orders
If you keep the inventory tracked and organized, you will avoid the urgent orders and extra costs, by paying the express delivery. You know what’s running low, and you can plan ahead.
3. Better Budget Control
We all want to keep the budget under control, right? With a clear overview of what you have, and what you actually use, it's easier to avoid ordering duplicates. You will also avoid buying things that are never used and stick to your budget.
4. More Efficient Teams
Your team will have more time to do the “useful” job, instead of wasting time by searching for parts or checking if something’s available. If the tools and the spares are in the right place, and if your team has that written down, or even better in the app, they will focus on doing their job.
5. Longer Equipment Life
Preventive and predictive maintenance, alongside MRO will help you reduce the number of breakdowns and ensure longer life of your machines and assets. This will help you save the money, long term..
6. Better Decision-Making
When MRO is tracked properly, the data tells you what’s working and what’s not. You will know which machines need the most repairs and what parts are used the most. With that information, you can improve your process.
Real-Life Example: MRO in Action
Let’s take a look at how proper MRO management can make a real difference. This example is based on a typical mid-sized manufacturing company. This company has several production lines and is often facing the pressure to reduce downtime.
One of the packaging lines was having issues often. Every time the machine went down, technicians lost 1–2 hours just guessing which part was needed, where it was stored and sometimes they even had to make a last-minute order..
Additionally, the company didn’t have a centralized list of what spare parts were available. Some were stored near the line, others in warehouses. Some parts were in “unknown-plance”, which only one technician knew. This guy “always remembered where things were.”
All of these were triggers to take MRO more seriously. Here’s what they did:
- Mapped out critical equipment and identified which parts fail most often.
- Set up a basic CMMS to track parts usage and stock levels.
- Organized the storeroom with labels and consistent part numbers.
- Created min/max levels for essential spares, so items were reordered before they ran out.
- Trained the team to log parts used and report low stock.
As you can see, none of these steps are complicated. The company gave the team time to make them a daily habit.
After few months, they’ve got he following results:
- Average downtime on that packaging line dropped by over 40%.
- Fewer emergency orders, which led to lower costs and less stress.
- Increased response time
- Technicians worked more on preventive work, instead of firefighting.
- Most importantly: less frustration. No more guessing where parts were or waiting days for a €5 component to arrive.
MRO in the Age of Digital Transformation
MRO isn’t immune to digital trends. The truth is, the way your maintenance team works and you manage the MRO is also affected by smarter, data-driven systems. Tools like IoT, AI, and cloud-based CMMS systems aren’t just buzzwords anymore. They’re part of every company that has factories, warehouses and service teams across industries.
IoT: Real-Time Visibility
Sensors can now track equipment performance 24/7: Starting from the temperature, all the way to the vibration. That data is then stored into the system and alerts the team before something breaks.
Of course, this will work only if you have the MRO ready to support it. If a sensor flags an issue and the needed part isn’t available, you’re still in trouble. Predictive tools are powerful, but they still rely on solid MRO inventory behind the scenes.
AI and Machine Learning
These tools can analyze usage patterns and predict which parts are most likely to get broken and when. This will help your team organise the purchase better and ensure stock levels are in place.
Instead of reactive decisions (“we’re out of this part again”), you get proactive suggestions (“you’ll likely need this in three weeks”).
Cloud-Based CMMS
Modern maintenance systems make it easy to track MRO in real time. CMSS systems like Serwizz help you organize the team no matter if they are on different sites or even countries. Everyone sees the same data: what’s in stock, what’s been used, what’s due for reorder.
It means fewer gaps in communication and faster decisions.
Conclusion: Why MRO Deserves More Attention
MRO is still not getting enough attention or the big budgets. However, if it is done right, it keeps everything else running.
Whether you’re managing a facility, running a production line or supporting a maintenance team, MRO is there. It’s part of your uptime, efficiency, cost control, safety and team performance.
When it’s managed well, nobody will notice it, which is exactly when we want. That’s it there without being an additional load to the team. With well implemented MRO you can avoid delays, extra costs and most importantly reduce the level of stress.
So if there’s one takeaway here, it’s this:
Good MRO isn’t just about parts and tools: it’s about keeping operations smooth, steady and ready for what’s next.