Facility
·
11 min read
Work Order Management for HVAC Maintenance
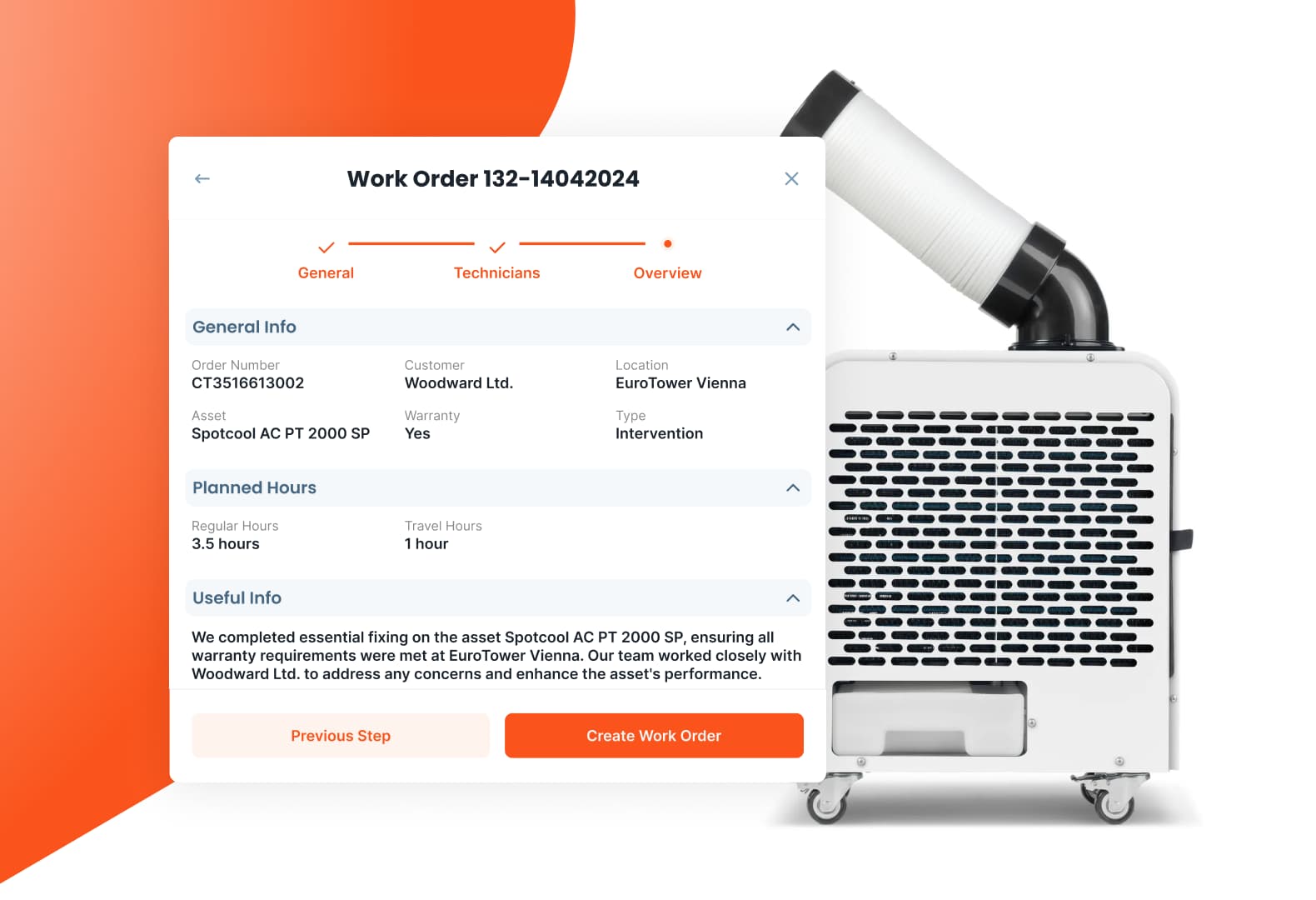
Challenges in HVAC Facility Maintenance
A couple of months ago, we were approached by a company specializing in technical maintenance and servicing of HVAC systems. Known as a leader in their industry, they had built a strong reputation over the years. But like many companies, they started struggling with the growing number of service requests and the lack of a clear maintenance work order process. Keeping everything organized had become a challenge and it was slowing them down.
The biggest issue for them? Work requests were coming in from all directions: mostly by phone, some through an online form, and occasionally, people would just drop by the office. It was all over the place. There wasn’t a clear, centralised system in place, which resulted in the following: the details were often missed or written down differently depending on who took the call. Sometimes even the person who took the notes was not sure what was written. Over time, this led to delays, a mess, and a lot of frustration on both sides: the customers, but also the employees.
As the volume of maintenance work kept growing, so did the operational bottlenecks. The company needed a smarter way to manage everything from receiving a work order request to completing and reporting on the service.
Discovery Phase: Listening to Every Role
When the client first approached us, it was clear that Serwizz already covered most of what they were looking for. The platform ticked many of the boxes they wanted: structured work order management, easy assignment of tasks, and visibility across the board. But to really make it work the way their team operates day to day, we needed to take a closer look.
That’s where the Discovery phase came in.
To get started, we organized a series of Discovery workshops. These sessions included not just upper management, but also the people who would actually use the system every day: administrative staff who log requests, service coordinators, finance and procurement teams, and most importantly, the field technicians.
We believe this is one of the most critical parts of designing any software: listening to every user group. This helps us understand the different workflows, pain points, and needs across the company. By listening to everyone involved, we could identify what needed to stay, what needed improving, and where a few smart customizations would make all the difference.
Because that’s the core idea behind Serwizz — unlike many other platforms, it adapts to your existing workflows, so you don’t have to change the way you work just to go digital.
From Discovery to Customization: Building the Right Tools
After gathering feedback, we compared user expectations and identified common goals. As mentioned, the Serwizz platform already had many powerful features, but to truly fit the company’s workflow, we built customizations specific to how they operate.
One major improvement was the centralization of work order management. In the old system, service requests were transcribed manually into spreadsheets or physical documents. In the new app, everything starts digitally. Now, when a work order request comes in, it’s logged directly into the system. A manager can quickly review the request, create a work order, assign it to a technician, and set a priority — all in just a few clicks.
The work order system standardizes terminology across the board. Everyone refers to the same parts, procedures, and service categories. This eliminates confusion and ensures that technicians and coordinators are always on the same page.
Technician View: Streamlined On-Site Work
From the technician’s perspective, the new system makes daily tasks much easier. Each technician receives their assigned maintenance work orders in the app, organized by date and urgency. They can clearly see what needs to be done for each job — no more calling the office to ask for instructions.
When on-site, technicians can take and upload photos before and after repairs. They can keep track of their time entries - including both working hours, travel time, and add notes, all of that, directly from their phone. This gives managers insight into the technician’s activity and allows for better planning and resource allocation.
Once the job is complete, the technician can complete the work order and go home. Why? Well, now they can capture the client’s digital signature and generate a service report with just one click. After a long day, there’s no need to go back to the office and do the paperwork. This speeds up the workflow and allows technicians to focus on their next task without unnecessary delays.
The app was created in a way that it supports both English and Croatian (and other languages can be supported as well), this turned out to be a crucial feature since part of the workforce comes from abroad. Whether someone is reviewing a work order example, entering materials used, or finalizing a report, everything is presented in their preferred language.
Manager View: Operational Oversight in Real Time
For managers, the application provides complete visibility into company operations. They can track every maintenance work order from submission to completion. It’s easy to see which tasks are pending, in progress, or closed.
Inventory tracking is also built into the system. Managers can monitor the usage of parts and materials, check stock levels, and receive alerts when it’s time to reorder. This reduces the risk of running out of essential components or overstocking items that rarely get used.
Another standout feature is equipment service history. For every piece of equipment, the system keeps a detailed maintenance log. Managers get automatic reminders when preventive servicing is due — helping to reduce breakdowns and extend the life of assets.
Time-tracking tools provide additional insights. Managers can evaluate technician performance based on actual hours worked and jobs completed. This helps identify top performers and also reveals areas where extra training or support may be needed.
All client and partner information is stored in a searchable database. Contracts are linked to accounts and automatically flagged when they are about to expire, giving the sales or account team time to take action.
Client View: Full Transparency and Self-Service
Clients also benefit greatly from the new system. Through a dedicated partner portal, they can submit a work order request, upload details, and check the status of their maintenance work order at any time. This self-service approach significantly reduces the number of phone calls and emails asking for updates.
Clients appreciate being able to see the entire service process unfold in real time. It gives them confidence that their requests are being taken seriously and addressed quickly. By providing work order examples and progress updates, the company has improved its customer relationships and increased satisfaction across the board.
Added Value: Offline Mode and Deep Analytics
Another big advantage is offline mode. While we are used to having connections anywhere and at any time, still many service locations have poor or no internet connection. With our app, technicians can continue their work as usual, as the data will be saved locally in the app and synced once a connection becomes available.
In manager view, this application comes with a useful but intuitive analytics dashboard that gives managers and team leads a clear overview of what’s going on. They can check things like how quickly teams are responding, how many work orders are still open, which clients need the most support, and how each technician is performing. With built-in filters, it’s easy to find exactly what you’re looking for without any effort. The manager can finally focus on real data, instead of collecting it. These insights help spot problems early, track what’s working, and keep improving the way the team delivers service.
What Is a Work Order, Really?
A work order is not just a task list, in short it's a structured way to request, plan, execute, and document maintenance or service work. Whether it’s a routine maintenance job or an emergency repair, a work order provides accountability, traceability, and clarity for everyone involved.
With modern facility maintenance work order software like Serwizz, businesses can reduce human error, speed up response times, and deliver better results — all while keeping managers, technicians, and clients in the loop.
To learn more, check out these helpful resources:
Conclusion: Real Results for Real Work
In the end, this company did what many hesitate to do: They did their own retrospective, assessed how things were working (or not working) and decided it was time for a change. By teaming up with us and customizing a system around their actual day-to-day needs, they didn’t just fix a few issues, they’ve managed to completely change how they run their business.
Now, they’ve got a clean and simple app that works for everyone in the chain: the technicians out in the field, the managers back at the office, and the clients who just want to know when their issue will be fixed. It’s not flashy, but it gets the job done: and that’s what really matters.