RACI
·
19 min read
What Is Responsibility Assignment Matrix (RACI)?
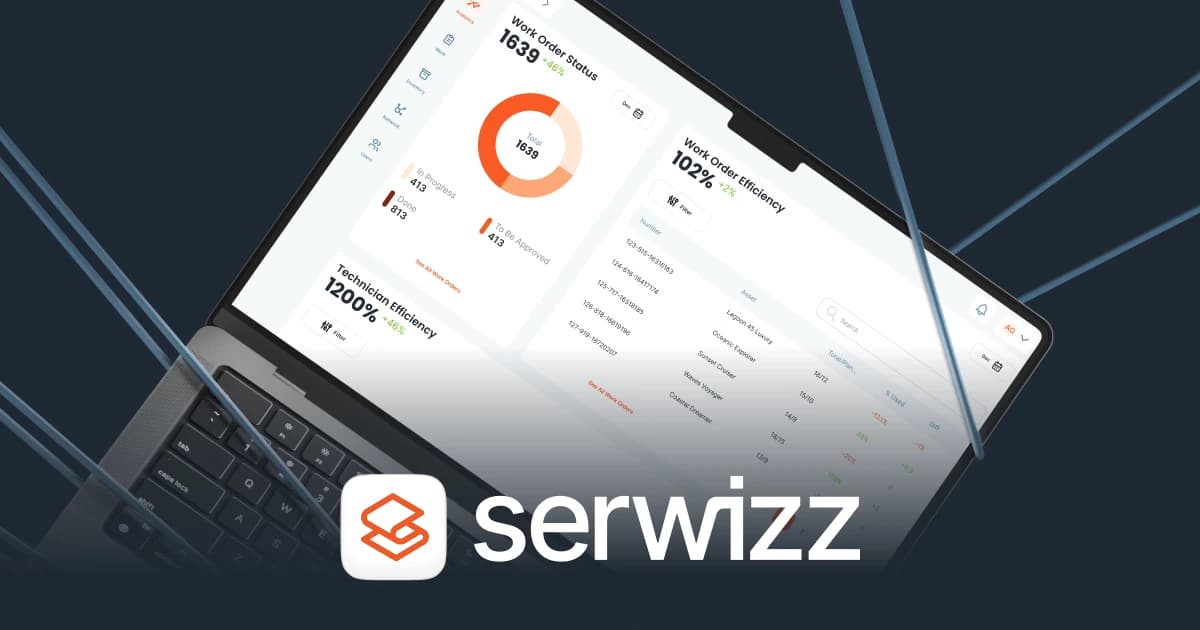
A responsibility assignment matrix (or just a RACI matrix) is a tool that clarifies roles and responsibilities within a team. It defines who is Responsible, Accountable, Consulted and Informed for each task.
Picture this: you’re in the middle of a maintenance emergency and wondering — who’s supposed to do what? As time ticks away, you’re asking yourself questions like: Who approves the fix? Who orders the broken part? Who should I inform? Trust us, these situations happen more often than you think in the maintenance world.
Luckily, there is a powerful tool - Responsibility Matrix. RACI matrix prevents those questions, so when your machine has issues, or down time, your technicians will know their job. No more finger-pointing. No more delays.
In maintenance, where timing is everything and downtime costs money, a Responsibility Matrix isn’t just a nice-to-have — it’s a must-have. It keeps workflows smooth, teams aligned, and operations running.
In this blog, we’ll break down what a Responsibility Matrix really is, how it works, and how you can create one that fits your maintenance team — without the usual headaches.
Key Components of the RACI Matrix
The RACI matrix is a framework that divides responsibilities into four simple roles. The key to successful maintenance operations is to fully understand these roles. By knowing the difference between the roles, you will clearly know who has the ownership and there will be no more guessing.
R — Responsible
This is the person (or group) who actually does the work. In the maintenance world, the responsible person could be the technician doing the repair, the manager who schedules the task or the person in finance who orders the parts. Note, that you can have more than one responsible person, but usually the less is better.
A — Accountable
This role is the ultimate owner of the task or decision. The Accountable person signs off that the job is done properly. They’re the go-to if something needs escalating. In maintenance, this could be the maintenance manager or team leader. Important: there should only be one Accountable per task to keep clear ownership.
C — Consulted
This role includes experts or stakeholders who offer their advice, before a decision or action happens. Think of the engineer giving guidance on a complex repair or the safety officer checking compliance. Their feedback is valuable but they don’t do the actual work.
I — Informed
This role includes people that need to be kept in the loop after the task is done or a decision is made. For example, the operations team might be informed about equipment downtime or the finance team about parts orders. They don’t have a direct role in execution but need updates to do their jobs well.
If you divide your tasks by using the RACI matrix, you can avoid assumptions, like “I thought someone else was doing that”. You can improve the team communication and keep everyone on the same page — which is critical when downtime is ticking.
Role | Who? | What They Do | Example in Maintenance |
---|---|---|---|
Responsible | The doer(s) | Performs the task or work | Technician repairing a machine |
Accountable | The owner | Ultimately owns the task and approves completion | Maintenance manager signing off the repair |
Consulted | Experts or advisors | Provide input or advice before the task or decision | Engineer advising on complex repair details |
Informed | Stakeholders needing updates | Kept up-to-date on progress or results after the task is done | Operations team informed about equipment downtime |
RACI vs RASCI vs DACI: What’s the Difference?
RACI matrix is a great tool, but sometimes maintenance teams face more challenging tasks or decisions. To help you pass these challenges, there are two more frameworks RASCI and DACI. We will now share an overview of each of these, so that you can make a right decision and choose the right one.
RACI — the classic
- R = Responsible (does the work)
- A = Accountable (owns the outcome)
- C = Consulted (provides input)
- I = Informed (kept updated)
Simple and effective. perfect for most maintenance tasks where roles are clear and decisions straightforward.
RASCI — a bit more detailed
This adds an S for Supportive.
- S = Supportive (helps with the work)
In maintenance, this could be the warehouse team who supplies parts or a specialist technician who assists during repairs but isn’t the main doer. RASCI helps when there’s a bigger team with clear helpers, not just doers.
DACI — focused on decision-making
- D = Driver (drives the task or project forward)
- A = Approver (gives final approval)
- C = Contributors (give input)
- I = Informed (updated on progress)
DACI is more about decision-making processes than task execution. Use it when you have complex approvals or multiple stakeholders involved in decisions, such as choosing a new maintenance technology or vendor.
Framework | Role | Description | Maintenance Example |
---|---|---|---|
RACI | Responsible | Does the work | Technician fixing equipment |
Accountable | Owns the task and signs off | Maintenance manager approving the repair | |
Consulted | Provides input | Engineer advising on repair details | |
Informed | Kept updated | Operations team notified about downtime | |
RASCI | Responsible | Does the work | Technician performing the repair |
Accountable | Owns the task and approves | Maintenance manager | |
Supportive | Helps with the work | Warehouse team supplying parts | |
Consulted | Gives advice | Safety officer reviewing compliance | |
Informed | Kept updated | Finance team informed about repair costs | |
DACI | Driver | Drives the task/project forward | Project lead managing a new maintenance system |
Approver | Gives final approval | Operations director signing off on the project | |
Contributors | Provide input | Technical experts advising on project decisions | |
Informed | Kept updated | All stakeholders updated on progress |
Which one should you pick?
- If your maintenance work is mostly task-driven and about getting things done — stick with RACI. It’s simple and covers most day-to-day needs.
- If you often rely on specialists or support roles to get a task over the line, RASCI adds a bit more clarity without overcomplicating things.
- If you’re dealing with bigger decisions, cross-team projects, or anything with lots of opinions flying around, DACI might be the better fit — it’s built for faster decision-making.
Benefits of RACI
Using a RACI matrix in maintenance isn’t just some buzzword. It actually makes your workday easier and helps get things done faster. Here are some of the benefits:
1. Clear accountability
Everyone knows who’s doing the job, who’s approving it and who just needs to stay informed. No more guessing.
2. Less downtime
When roles are clear, approvals and tasks don’t get stuck waiting. Machines get fixed faster and your operation keeps moving.
3. Better communication
The right people get consulted early and the right people get updates later. No one’s left in the dark.
4. Fewer misunderstandings
No blaming or finger-pointing because everyone knows their role and what’s expected.
5. Easier planning
You can schedule your team better and make sure you have the right parts and skills lined up before the work starts.
6. Works as you grow
Whether you’re a small team or a big operation, RACI helps you keep things organized as things get more complicated.
Limitations of RACI
Just like any other tool RACI is not perfect. Especially in the fast-paced world of maintenance. Here are a limitations:
1. Doesn’t show task priority or timing
RACI tells you who’s involved but not when tasks should happen or how urgent they are. You’ll still need other tools to manage schedules and priorities.
2. Can get complicated with big teams
When many people are involved, the matrix can become a mess. Too many Responsible or Consulted roles can cause confusion instead of clearing things up.
3. Doesn’t handle overlaps well
Sometimes tasks overlap or change quickly, especially in emergency repairs. RACI can struggle to keep up if roles shift on the fly.
4. Risk of “Accountable” overload
If too many tasks assign the same person as Accountable, it creates bottlenecks. Clear delegation beyond just RACI is important.
5. Needs buy-in and upkeep
If the team doesn’t actually use or update the matrix, it becomes useless. Like any tool, it only works if everyone takes it seriously.
Steps to Create a RACI Matrix
Creating a RACI matrix doesn’t need to turn into a week-long project. You don’t need fancy tools or a consultant to get started. Most teams can build one in a short workshop or during a regular planning session. Just gather the right people, focus on your real workflows and keep the conversation grounded in how things actually happen — not how they should happen on paper.
Here’s how to build a RACI that actually works:
1. List the key tasks or activities
Start by identifying the main tasks in your maintenance workflow. These could include things like:
- Scheduling preventive maintenance
- Approving work orders
- Ordering spare parts
- Responding to maintenance breakdowns
- Conducting audits
- Doing the inspections
Focus on the tasks where confusion often happens or where multiple roles are involved.
2. Identify the roles involved
Don’t list names — list roles. Stick to job titles or functions. For example:
- Technician
- Maintenance Planner
- Maintenance Manager
- Warehouse or Stores
- Finance
- Approver
If you're working in a smaller team, one person might wear multiple hats — and that’s fine. Just keep the matrix role-based so it scales as your team grows.
3. Assign R, A, C, and I for each task
Now go down the list task by task and assign the appropriate roles:
- R – Responsible: Who will actually do the task?
- A – Accountable: Who owns the outcome and makes sure it gets done?
- C – Consulted: Who should give input before or during the task?
- I – Informed: Who just needs to be kept in the loop?
Remember: There should only be one Accountable per task. More than one, and you’re back to confusion.
4. Keep it tight and realistic
It’s easy to start adding too many names under Consulted or Informed — but more isn’t better. Just because someone is slightly involved in the process doesn’t mean they need to be looped into every update. Ask yourself: Does this person really need to be updated? Will it help get the job done faster or better? If not, leave them out.
Too many C’s and I’s just slow things down.
5. Review and agree as a team
Bring the team together — don’t just build the matrix alone at your desk. Explain the roles and tasks, ask questions and make sure everyone agrees. This is where a lot of misunderstandings get cleared up early.
If people disagree about who’s responsible or accountable — great! Better to resolve it now than during a breakdown at 2 a.m.
6. Share it and use it
Once everyone agrees, put the matrix where it’s visible and easy to access — on a shared drive, in the CMMS, or even printed and pinned on the wall. And most importantly: use it.
- Use it during planning meetings
- Use it when assigning work orders
- Use it when something breaks and roles are unclear
A RACI matrix only works if it becomes part of how your team communicates and makes decisions.
Practical Examples of RACI in Maintenance
It’s one thing to understand RACI in theory — it’s another to see how it works in real maintenance tasks. Here are two everyday examples where a RACI matrix can clear up confusion and save time:
Example 1: Emergency Repair
Scenario: A conveyor belt in a distribution center breaks down during peak hours.
Task | Technician | Maintenance Lead | Warehouse | Safety Officer | Ops Manager |
---|---|---|---|---|---|
Diagnose issue | R | A | |||
Approve emergency repair | A | C | C | ||
Order replacement part | R | A | |||
Notify operations of downtime | I | ||||
Restart operations after repair | R | A | C | I |
Notes:
- The technician does the work (Responsible), but the maintenance lead signs off and keeps it moving (Accountable).
- Safety and ops give input (Consulted), but don’t slow the process.
- Ops is informed, not involved in execution.
Example 2: Scheduled Preventive Maintenance
Scenario: Monthly PM on HVAC system in a hospital wing.
Task | Technician | Maintenance Planner | HSE Officer | Facility Manager | Finance |
---|---|---|---|---|---|
Schedule PM | R, A | C | |||
Perform maintenance | R | ||||
Review safety procedures | A | C | |||
Order and track spare filters | R | A | |||
Log completed work in CMMS | R | I | I |
Notes:
- The planner drives the schedule, while the technician handles the work.
- Safety procedures go through HSE, and the finance team needs to be informed for tracking costs.
- CMMS updates keep the rest of the team in the loop.
Best Practices for RACI: DOs and DON’Ts
A RACI matrix is only helpful if it actually gets used. With these DOs and DON’Ts you can avoid common mistakes.
Responsibility Matrix DO’s
1. Make it role-based, not name-based
Use job titles rather than people’s names. People change — roles don’t.
2. Make it visible
Don’t let your matrix collect dust in a forgotten spreadsheet. Print it and put it on the wall or even better put it in the CMMS. If your RACI is not visible, it’s not useful.
3. Limit Accountables to one per task
One task = one person accountable. Anything else creates confusion or finger-pointing.
4. Review it regularly
Maintenance processes change. So should your RACI. Revisit it during team retros, audits, or when something feels “off.”
5. Use it during planning and post-mortems
When you’re building out a new process or reviewing a breakdown, pull out the matrix. It shows who should’ve done what — and where the gaps were.
Responsibility Matrix DON’Ts
1. Don’t overcomplicate it
If every task has five Consulted and three Informed, you’re slowing things down. Only include roles that truly need to be there.
2. Don’t skip the team discussion
A RACI made in isolation won’t stick. Build it together, or at least review it together — people need to buy in.
3. Don’t treat it as set in stone
It’s a living tool, not a contract. If roles shift or someone’s overwhelmed, adjust it.
4. Don’t confuse Responsible with Accountable
This is a classic mistake. The Responsible does the work. The Accountable owns the result. They’re not always the same person.
Get these basics right, and your RACI matrix becomes more than a document — it becomes part of how your team works.
Final Thoughts
The truth is: in maintenance, problems rarely show up at the perfect time. When they hit, your team needs to know exactly who’s handling what. No guessing, no delays.
A RACI matrix might look simple, however it has a huge impact. It keeps your team aligned, avoids double work and speeds up decisions. No matter if you're planning preventive work, dealing with the breakdowns or managing spare parts, RACI gives you a framework to stay organized and clear.
You don’t need to overthink it. Build your first matrix based on real tasks, adjust as you go and make sure your team actually uses it. The goal is to achieve clarity.
Because in maintenance, clarity means less downtime, and less downtime means everything keeps moving.
Next Steps
👉 Learn more about Serwizz CMMS
👉 Book a demo or get started free